Battery Weld Inspection Solutions
Take Battery Performance to the Next Level
MoviTHERM’s battery weld inspection system is an out-of-the-box solution for in-line monitoring of battery electrode and cell welding processes. Leveraging infrared camera technology, the battery weld inspection system provides fast and reliable non-contact measurements to maintain proper temperatures across the entire welded surface, resulting in a high-quality, low-resistant connection.
Battery Weld Inspection Solutions
Take Battery Performance to the Next Level
MoviTHERM’s battery weld inspection system is an out-of-the-box solution for in-line monitoring of battery electrode and cell welding processes. Leveraging infrared camera technology, the battery weld inspection system provides fast and reliable non-contact measurements to maintain proper temperatures across the entire welded surface, resulting in a high-quality, low-resistant connection.
Optimize Performance
Ensure Safety
Protect Brand Reputation
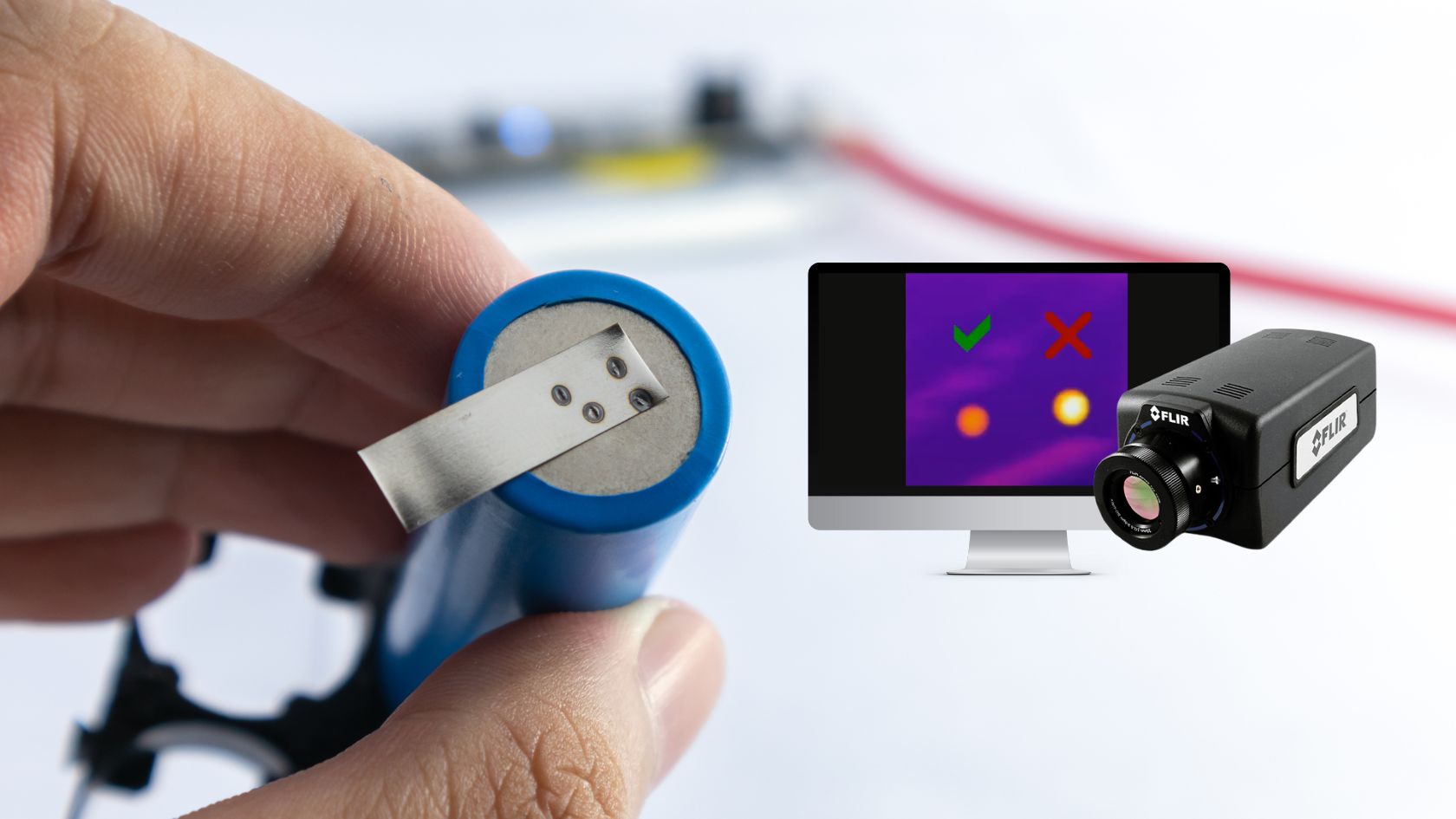
Ensure High-Quality Battery Welds
If you’re involved in the production or utilization of batteries, this is the place to discover how active thermography can revolutionize your operations. Our advanced technology harnesses the power of thermal imaging to optimize battery life and performance by guaranteeing high-quality welds. Our system ensures the utmost reliability, safety, and efficiency in your battery-related endeavors..
Using Active Thermography for Quality Inspection
Active thermography offers superior effectiveness for battery weld defect detection compared to passive thermography. While both methods utilize infrared imaging, active thermography deliberately introduces external energy to stimulate thermal responses.
The controlled excitation generates significant thermal contrasts between the defect and the surrounding material. Active thermography enhances the detection sensitivity, making it more proficient at identifying subtle defects that may be challenging to detect with other inspection methods.
Type of Defects That Can Be Detected
Benefits of Infrared Battery Weld Inspection
Ensure High-Quality Battery Welds
If you’re involved in the production or utilization of batteries, this is the place to discover how active thermography can revolutionize your operations. Our advanced technology harnesses the power of thermal imaging to optimize battery life and performance by guaranteeing high-quality welds. Our system ensures the utmost reliability, safety, and efficiency in your battery-related endeavors.
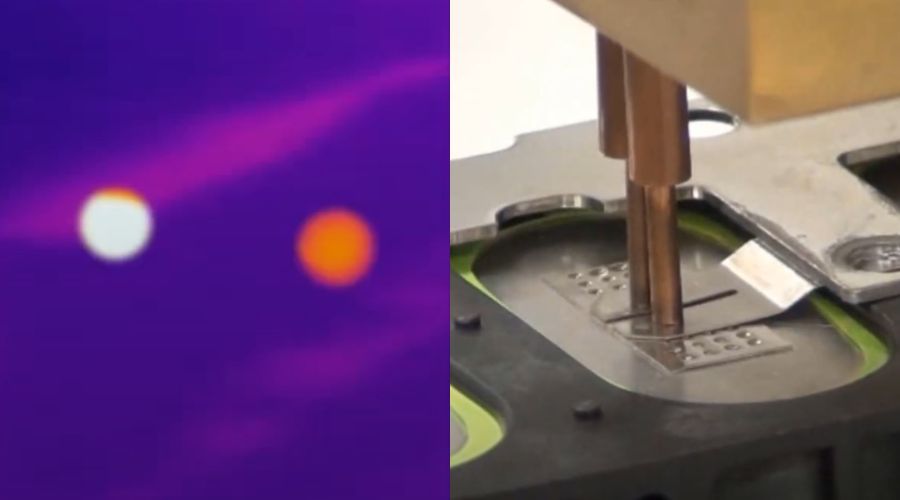
Type of Defects That Can Be Detected
Benefits of Infrared Battery Weld Inspection
How does the system work?
BWI uses Active Lock-in Thermography (LiT) which consists of applying a periodic electrical signal to the battery and monitoring the resultant temperature variation with a synchronized thermal camera. The electrical signal is applied by an external power supply or the source load during the end-of-line load test. A computer captures multiple IR images and applies a processing algorithm to produce a surface map identifying localized hotspots. LiT produces images with greater resolution and temperature distribution over passive IR thermography.
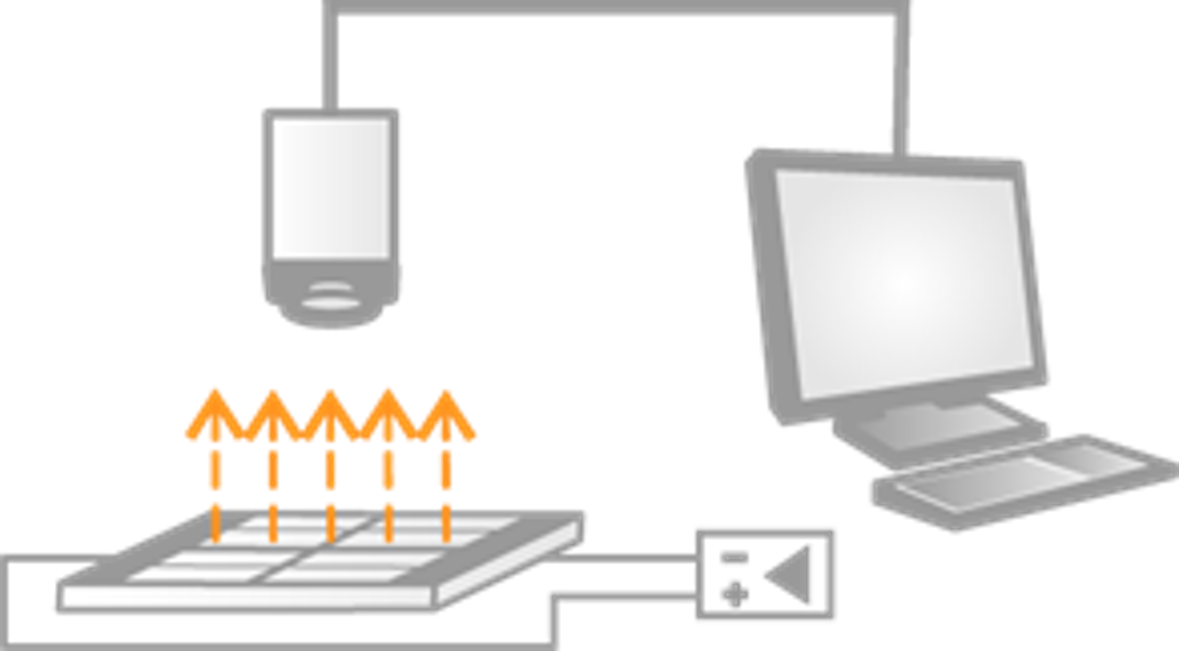
Active vs. Passive Thermography
Active thermography offers several advantages over passive thermography for battery weld quality inspection. Here are the key advantages of active thermography:
Supported Infrared Cameras
Teledyne FLIR® A6781 | Teledyne FLIR® A8581 | Teledyne FLIR® X8581 | |
---|---|---|---|
![]() |
![]() |
![]() |
|
Resolution | 640 x 512 | 1280 x 1024 | 336 x 256 / 640 x 512 |
Full Frame Rate | Programmable; 0.0015 Hz to 125 Hz (GigE), 60 Hz (CXP) | Programmable; 0.0015 Hz to ~45 Hz | Programmable: ~0.5 Hz to 181 Hz |
Standard Temperature Range | -20°C to 350°C (-4°F to 662°F) | -20°C to 350°C (-4°F to 662°F) | -20°C to 350°C (-4°F to 662°F) |
Optional Temperature Range | 45°C to 600°C (113°F to 1112°F) (ND1) 250°C to 2000°C (482°F to 3632°F) (ND2) 500°C to 3000°C (932°F to 5432°F) (ND3) |
45°C to 600°C (113°F to 1112°F) (ND1) 250°C to 2000°C (482°F to 3632°F) (ND2) 500°C to 3000°C (932°F to 5432°F) (ND3) |
45°C to 600°C (113°F to 1112°F) (ND1) 250°C to 2000°C (482°F to 3632°F) (ND2) 500°C to 3000°C (932°F to 5432°F) (ND3) |
Accuracy | ≤100°C (≤212°F), ±2°C (±3.6°F) accuracy (±1°C/1.8°F typical); >100°C ±2% of reading (±1% typical) | ≤100°C: ±2°C (±1°C typical), >100°C: ±2% of reading (±1% typical) | ≤100°C: ±2°C (±1°C typical), >100°C: ±2% of reading (±1% typical) |
Sensitivity | ≤20 mK (typical) | ≤30 mK (typical) | ≤30 mK (typical) |
*Specifications are subject to change without notice. 6/2023