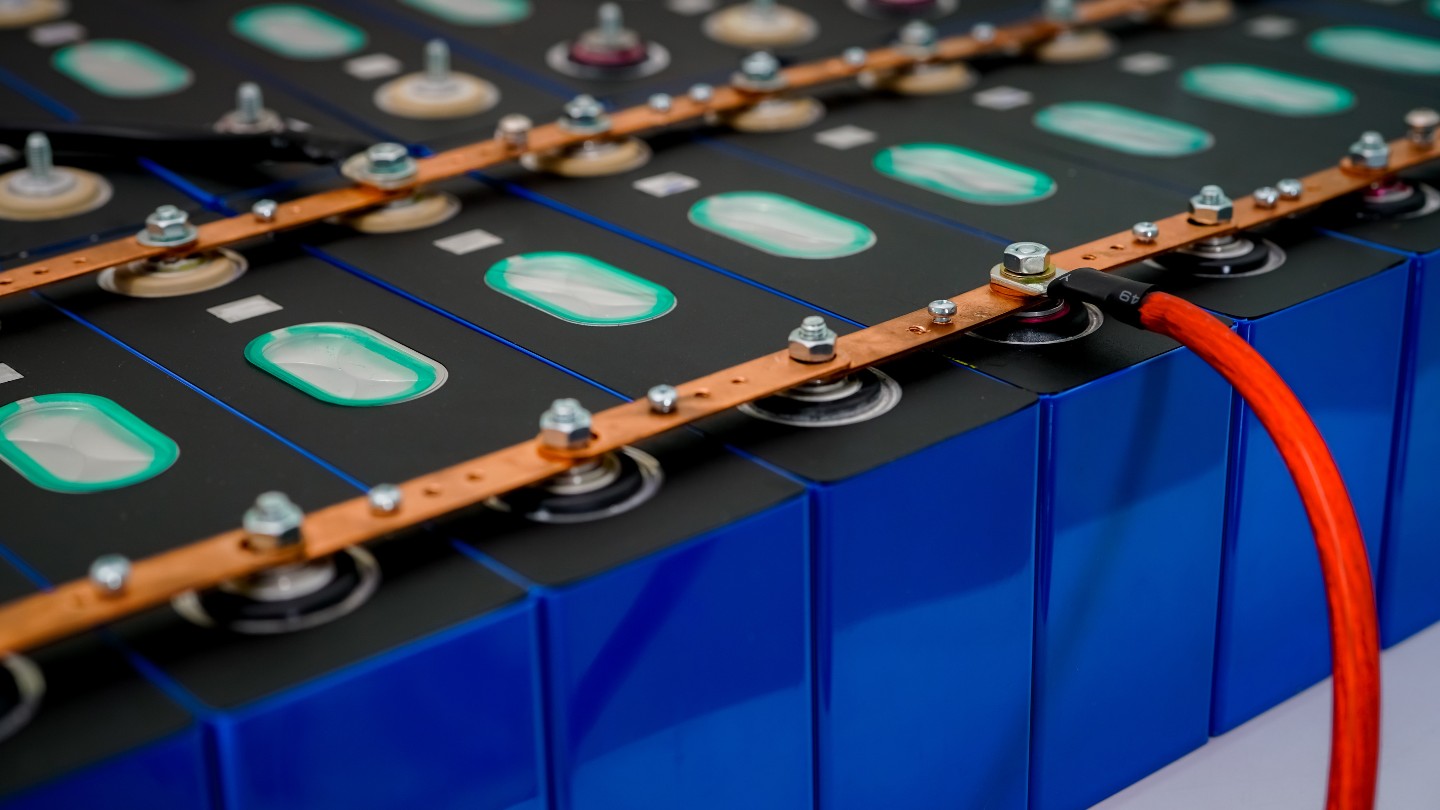
Using Infrared Thermography for Battery Inspection
Battery Inspection using Active Thermography becomes more important in order to stay competitive. Manufacturers of lithium-ion Batteries (LIB) are challenged with maximizing battery performance and minimizing costs to keep the adoption of LIB technology economically attractive.
From toothbrushes to automobiles, earbuds to mobile devices, and toys to semi-trucks, lithium-ion Battery technology is finding its way into just about everything. As such, the demand for battery materials, innovation in electrode design, improvements in manufacturing, and optimization of charge density are ever-increasing.
In this article, we discuss how active thermography and non-destructive testing (NDT) can be used for battery inspection at various stages of the manufacturing process to minimize electrode defects, optimize material usage, and ensure product quality.
Lithium-Ion Battery Anatomy
A lithium-ion battery consists of multiple parts with the cell acting as the primary component. The cell is the workhorse of the battery and is comprised of the following materials:
Current Collectors
The current collectors are the two battery ends with positive and negative connection points. These connections points are used for charging (power to) and discharging (power from) the battery.
Cathode
The cathode stores lithium and is the positive electrode made from a chemical compound metal oxide.
Anode
The anode stores lithium and is the negative electrode typically made from carbon.
Separator
The separator restricts the flow of electrons inside the battery but allows for lithium ions to pass back and forth from the cathode and anode electrodes.
Electrolyte
The electrolyte fills between the electrodes and carries the lithium ions from the anode and cathode during charge and discharge.
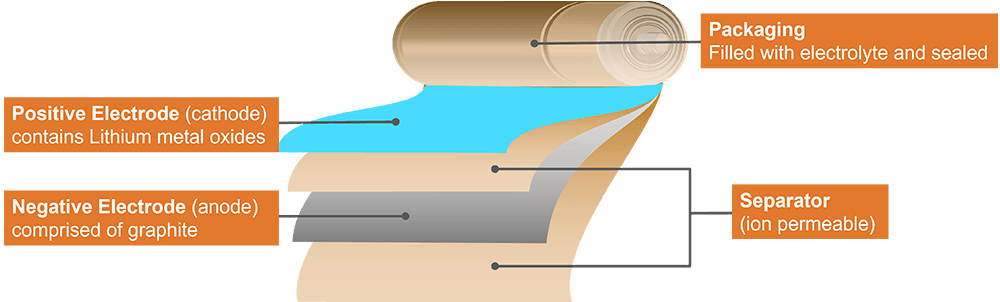
Battery Inspection Anatomy
Lithium-Ion Battery Operation
The operation of a lithium-ion battery is all about the back-and-forth movement of lithium ions between the cathode (+) and anode (-) electrodes. The ions move in one direction during charging (absorbing power) and in the opposite direction during discharge (supplying power). When the ions no longer flow the battery is either fully charged or discharged.
Charge Phase (Absorbing Power)
During the charge phase, with external power applied, lithium ions will migrate from the positive cathode to the negative anode through the separator and electrolyte. At the same time, electrons will flow from the cathode to the anode, however, unlike the lithium ions, the electrons cannot pass through the separator and take a different path around the outer circuit. Arriving at the anode, the electrons and ions combine. The battery is fully charged and ready to use when no more ions can flow.
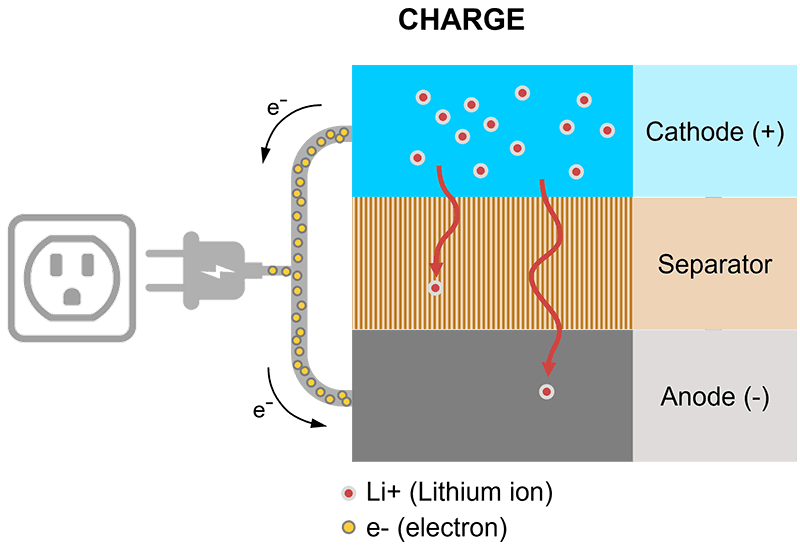
Battery Inspection Anatomy
Discharge Phase (Power From)
During the discharge phase, the lithium atoms in the anode are ionized and separated from their electrons. The lithium ions migrate through the separator and electrolyte from the negative anode to the positive cathode. Simultaneously, the free electrons flow from the anode to the cathode electrode via the outer circuit, providing power to an external device like a laptop computer. The ions and electrons recombine at the cathode becoming electrically neutral. The battery is fully discharged when no more ions can flow and needs charging to supply power again.
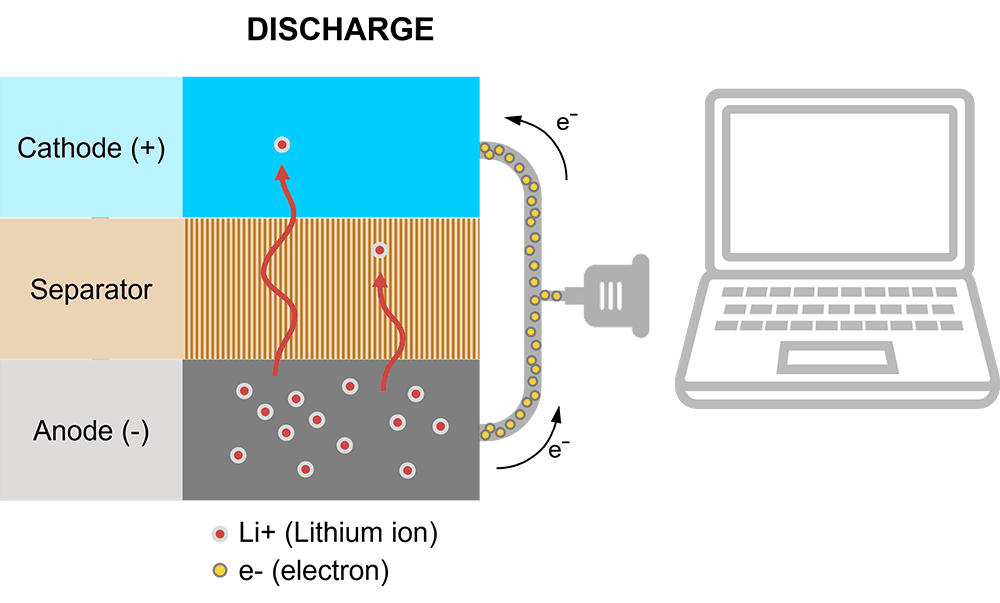
Battery Inspection Anatomy
Lithium-ion Battery Manufacturing Process
The following graphic illustrates the battery manufacturing process, which includes three major parts: electrode preparation, cell assembly, and battery electro chemistry activation.
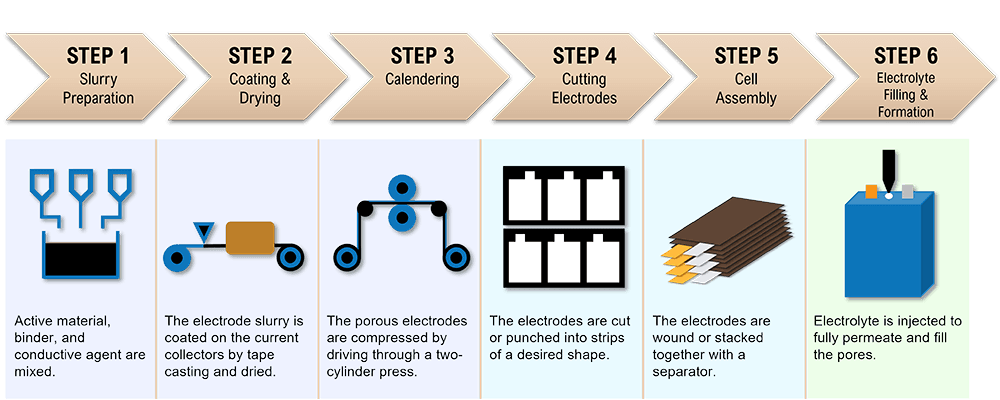
Battery Manufacturing Process
1. Slurry Preparation:
the active material (AM), conductive agent, and binder are mixed to form a uniform slurry with the solvent.
2. Coating and Drying:
The slurry is pumped into a slot die, coated on both sides of the current collector (Al foil for cathode and Cu foil for the anode), and delivered to drying equipment to evaporate the solvent.
3. Calendering:
The electrodes are compressed by driving through a two-cylinder press. This will help adjust the physical properties (bonding, conductivity, density, porosity, etc.) of the electrodes.
4. Cutting Electrodes:
The finished electrodes are stamped and slitted to the required dimension to fit the cell design. The electrodes are then sent to the vacuum oven to remove the excess water.
5. Cell Assembly:
After the electrodes are well prepared, they are sent to the dry room with separators for cell production. The electrodes and separator are winded or stacked layer by layer to form the internal structure of a cell. The aluminum and copper tabs are welded on the cathode and anode current collector, respectively.
6. Electrolyte Filling & Formation:
The cell stack is then transferred to the designed enclosure. Manufacturers use a variety of packaging depending on the cell application. The enclosure is filled with electrolyte before the final sealing and completes the cell production.
Battery / Electrode Performance
At a basic level, any factors that impact the travel of lithium-ions between the cathode and anode electrodes within a battery will impact performance of that battery. As such, the design, manufacturing, and operation of a battery should be to optimize ion and electron flow.
Within the manufacturing process there are instances when defects and flaws might be introduced into the battery product. For example, during the Coating & Drying step the forming electrodes become potentially susceptible to the following:
- Uneven compound spread/thickness variation
- Variation in carbon to polymer binder ratio
- Scratches
- Air bubbles/blisters
Other performance damaging factors can result from the introduction of contamination particles into the electrode foils. During coating, calendaring, and slitting electrode foils can be exposed to delaminated particles, abraded metallic particles, and dust from the production environment.
The introduction contaminants, defects, and flaws will adversely affect the ion / electron ability to travel within the electrochemical cell and thus reduce battery performance.
Active Thermography for Battery Inspection and Quality Control (QC)
IR Thermography has shown to be an effective non-destructive testing method for QC in multiple industries for various applications. The basic operation of an IR camera is based upon the heat transfer principle of radiation. The infrared camera has within it a focal plane array of detector elements that “see” infrared light radiated from object surfaces. The radiation captured by the infrared camera detector is digitized, converted to data, and displayed as an image that can be viewed in the visible spectrum. Certain infrared cameras are radiometrically calibrated to record and display measurement units. Infrared cameras are available with different sensors and pixel resolutions to see specific infrared wavebands.
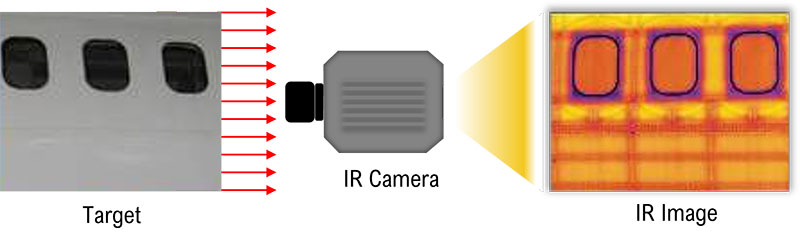
Advanced Thermography for Battery Inspection and Quality Control (QC)
Flash Thermography for Battery Inspection
Battery Inspection using active Thermography involves the excitation of the target and has been found to be most effective in the detection of flaws and contaminants of battery electrodes. Flash IR thermography is a form of active thermography where the target is exposed to a flash of thermal energy and the subsequent change in surface temperature is monitored by an IR camera. A thermal wave signal sequence is acquired by a computer with real-time image signal processing and analysis revealing how the thermal energy passes from the surface to the interior of the target. If the target has voids or defects, the thermal conduction paths will be disrupted. These disruptions lead to temperature differences on the surface that are detected by IR thermography.
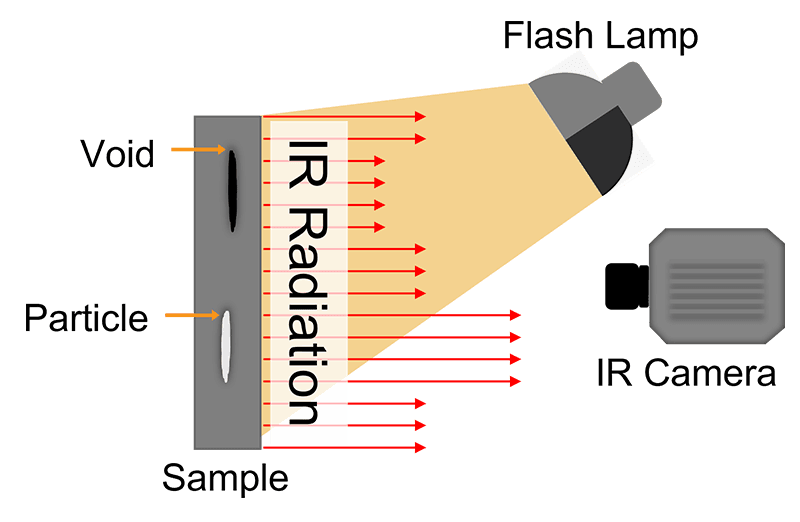
Flash Thermography for Battery Inspection
In general, an increase in the temperature profile suggests the presence of contaminants and agglomerates, while a decrease in the temperature profile indicates pinholes and blisters.
Another Battery Inspection application uses active flash thermography directly following the cell assembly stage where anode and cathode electrodes are welded together, and arrester tabs are attached. Welds are critical since they determine internal contact resistance which impacts charging times, power output, and heat generation. Additionally, weld strength against wear and fatigue will determine the lifetime of the battery.
By analyzing the heat propagation through the weld with advanced thermography, determinations can be made about the weld structure and electric conductivity. In general, high thermal conductivity indicates good welds that are uniform with good penetration and positive current flow.
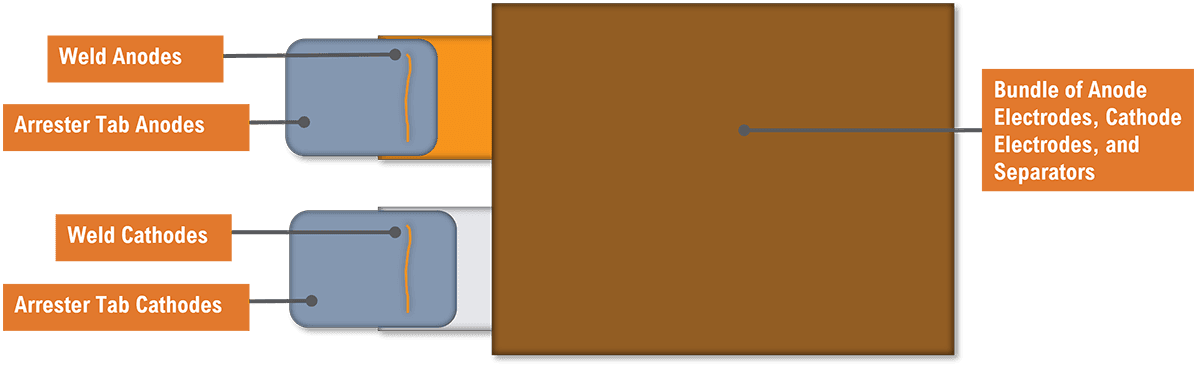
Battery Performance Detractors
Conclusion
Battery Inspection and Monitoring electrodes, cells, and batteries along the production path can help identify faults and defects early, allowing for quick production condition adjustment. Identifying product quality issues closer to generation points will reduce scrap, improve product quality, and optimize production costs.
Active thermography has proven to be an effective inline NDT method for evaluating and diagnosing the production of lithium-ion batteries. It can be used to identify the introduction of contamination particles and the formation of defects during the electrode creation stages. Additionally, Battery Inspection using active thermography can be an effective tool for evaluating welds in cell creation and battery packing.
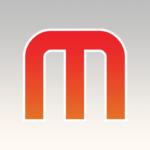
About MoviTHERM:
MoviTHERM – Advanced Thermography solutions was founded in 1999. The company offers solutions for plastic welding, package sealing, and non-destructive testing. In addition, MoviTHERM provides IoT Cloud monitoring solutions for thermal imaging applications for early fire detection, machine condition monitoring, and other applications. MoviTHERM is a Teledyne FLIR Premium Partner and master distributor for FLIR Thermal Cameras for automation and science applications.