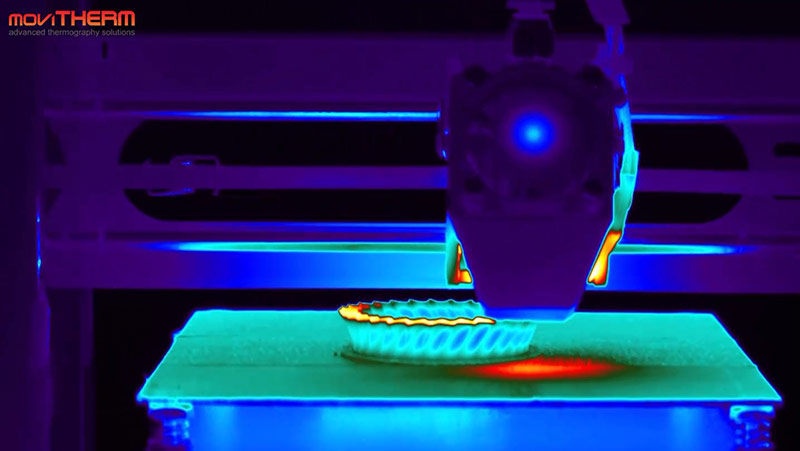
Advantages Thermal Monitoring Used for 3D Printing
Additive Manufacturing – an Overview
The world of 3D printing, otherwise known as ‘Additive Manufacturing’ (AM) has experienced a significant boost in recent years. The industry is forecasted to grow to approximately 10.8 billion dollars by 2021, up from 2.2 billion in 2012. Modern technology can now print everything from houses to machine parts in 3D. It is expanding well beyond the notion of everyday people printing their individual projects in their own homes into a sprawling industrial sector. 3D printing is massively increasing on an industrial scale.
NASA, for example, has designed two 3D printers to be sent into space to operate in zero gravity for the International Space Station. 3D is also being used in medical applications to create implants and prosthetics. Architectural elements are created to further design capabilities. A multitude of prototypes are being created every day across many industries. These are just as a few examples of the versatility of 3D printing.
Essentially, all 3D printing involves the laying down of various materials from polymers, metals, to fiber ceramics, layer by layer until the printing process is complete. There is a large degree of materials and methods available to print with dependent on the application the printed item is destined for. The various materials used include ABS plastics, PLA, polyamide (nylon), glass filled polyamide, silver, steel, titanium, photopolymers, and polycarbonate.
Additive Manufacturing Methods
A few of the methods used in Additive Manufacturing include the following:
- Fused Deposition Modeling, or FDM: Heats a thin filament of thermoplastic material depositing it layer by layer until the object is completed
- Large Scale Polymer Deposition: Heats polymer pellets to their melting point then extrudes these polymers layer by layer until the printing process is complete
- Laser Blown Powder Deposition (Laser Metal Deposition): Uses an inert gas to spray metal powder into a melt pool created by a laser.
- Electron Beam Melting: Melts metal powder in layers that are bonded with a computer -controlled electron beam.
- Selective Laser Sintering: Uses a high-powered laser to fuse small particles of plastic, metal or ceramic into a mass with 3 dimensional properties.
Additive versus Subtractive Manufacturing
The primary advantage of Additive Manufacturing is its cumulative creation process. This provides a much greater flexibility for producing complex geometrical shapes as opposed to taking a piece of raw material and removing from it to create what is needed.
When machining, milling, sawing, filings are involved, all these processes are considered ‘Subtractive Manufacturing’, sometimes called CNC, which produces a considerable amount of waste in comparison to an Additive Manufacturing process.
A 3D Printer Being Monitored by a Thermal Camera
However, both processes have their challenges. While Subtractive Manufacturing may be somewhat wasteful and limited to the “machinable” geometries, Additive Manufacturing also has its downside. Process parameters are much more difficult to control, primarily critical temperatures. Nevertheless, thanks to thermal imaging, Additive Manufacturing can be carefully monitored in order to produce a better product.
Parts manufactured using additive methods, such as 3D printing, can often involve imperfections in the manufacturing process creating issues like open voids, slippage between layers, thermal stresses, and to some extent crystallization of printed materials. Generally speaking, Additive Manufacturing requires a lot of trial and error during a new part setup. With thermal imaging, the printing extruder head and printed materials can be observed as the printing is taking place. This is helping to point out any issues in the process and can help operators fine tune their processes and create a better product.
Thermal Camera Selection for Additive Manufacturing
When selecting a thermal camera for measuring critical process temperatures, several factors need to be considered. First and foremost, the actual printing process and materials involved will determine, which type of thermal camera needs to be employed. For example, in a laser metal deposition application, very high temperatures are present, related to the melting temperature of the metal powders involved. This requires a thermal camera capable of measuring extremely high temperatures without saturating the image detector. Additionally, due to the rapid thermal conductivity in metals, a suitable thermal camera needs to have the capability of very short detector integration times. This is necessary in order to capture rapidly changing temperatures.
When dealing with polymer-based printing processes, these requirements are much more relaxed. Melt temperatures are much lower and so are thermal conductivity of these types of materials. This typically allows the use of much more affordable thermal imaging cameras with microbolometer type detectors.
Thermal imaging cameras can significantly improve the printing process, especially when integrated as a sensory feedback mechanism in a closed loop control for Additive Manufacturing processes. They can also dramatically reduce the setup time of the first article and perform in-situ process monitoring, control as well as quality assurance.
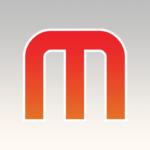
About MoviTHERM:
MoviTHERM – Advanced Thermography solutions was founded in 1999. The company offers solutions for plastic welding, package sealing, and non-destructive testing. In addition, MoviTHERM provides IoT Cloud monitoring solutions for thermal imaging applications for early fire detection, machine condition monitoring, and other applications. MoviTHERM is a Teledyne FLIR Premium Partner and master distributor for FLIR Thermal Cameras for automation and science applications.