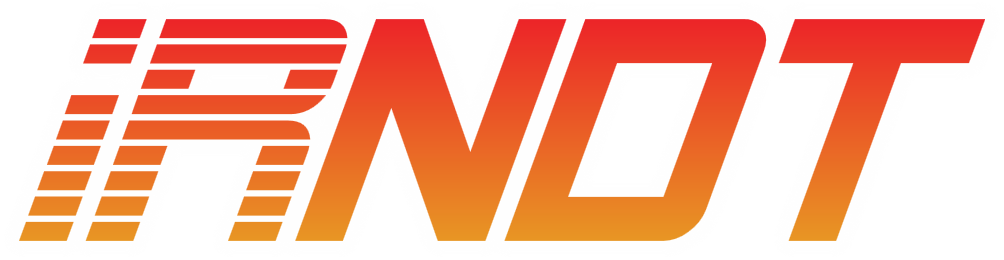
Infrared Non-Destructive Testing Solutions
For over 15 years, MoviTHERM has provided infrared NDT expertise and solutions to help engineers, researchers, and developers solve problems that cannot be resolved with traditional passive infrared test methods. MoviTHERM irNDT solutions use active excitation and intelligent algorithms to tease out the finest internal details of a material.
irNDT Measurement Principle – Active Thermography
Active thermography is an effective method for non-destructive testing of materials involving the induction of heat flow in a test object by external excitation. The heat flow within the test object is influenced by internal conditions and measured on the surface by an IR camera. This technique detects not only the smallest surface defects, but also internal structural defects under the surface.
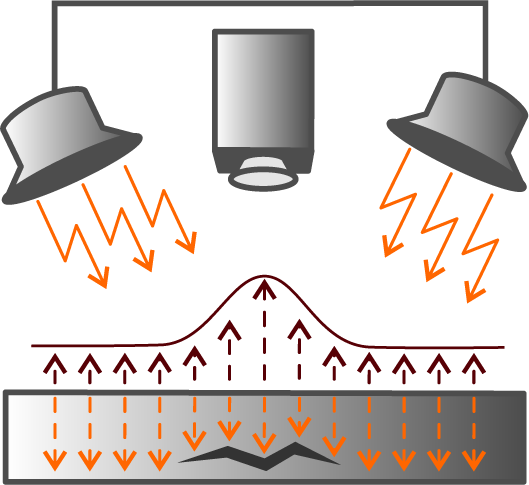
Active Thermography – irNDT Methods
Transient
Halogen light is used to create an extended heat excitation. Thermography analyzes the change in the thermal state of the target.
Flash
Xenon light provides a short and intense excitation that is analyzed with thermography. Is well suited for materials with high thermal conductivity and shallow defects.
Lock-In
A periodical excitation source is synchronized with the IR camera. The software generates an amplitude and phase image to indicate the location and nature of the defect.
Vibro
Ultrasound is used to excite the specimen. Friction between vibrating cracks creates heat signatures that are measured by the infrared camera.
Failure Analysis
A test specimen is excited with a periodic electrical signal and the resultant surface temperatures are captured by a synchronized thermal camera. Processing algorithms produce a surface map identifying localized hotspots.
Thermal Stress Analysis (TSA)
A test sample is stressed by modulating mechanical excitation with the induced infrared imagery converted into stress units.
Active Thermography – irNDT Excitation Sources
Halogen Lamp
Xenon Lamp
Laser
Eddy Current
Ultrasound
Materials You Can Inspect Using Active Thermography
Inspection Material | Detection | NDT Technique | Excitation Source |
---|---|---|---|
Composites | Surface defects, Internal subsurface defects, voids, disbonds, delaminations, water ingress. | Transient | Halogen Lamp |
Surface defects, delaminations, cracks, porosity, disbands. | Pulse | Xenon lamp with power source | |
Small surface defects, small subsurface defects, delaminations, voids, disbonds, inclusions. | Lock-in | Halogen Lamp | |
Metal | Welded Seams, corrosion, fatigue damage, inclusions, voids, cracks. | Pulse | Xenon lamp with power source |
Welded Seams, corrosion, fatigue damage, inclusions, voids, cracks. | Transient | Ultrasonic Horn Eddy current |
|
Fine defects, cracks, voids inclusions. | Lock-in | Ultrasonic Horn Eddy current |
|
Semiconductor | Cracks, shunts, delaminations, inclusions, voids, dislocations, defective junctions. | Lock-in | Halogen Lamp |
Microelectronics | Shorts, faulty components, current bleed. | Lock-in | Programmable Power Supply |
Micron size defects. | Lock-in | Laser | |
Batteries | Electrode contamination, coating thickness variation, cracks, fractures. | Pulse | Xenon lamp with power source |
Electrode tab weld quality, cell weld quality. | Lock-in | Programmable Power Supply | |
Ceramics | Cracks | Transient | Ultrasonic Horn |
How to get started
3 Steps to Confident IR Non-Destructive Testing
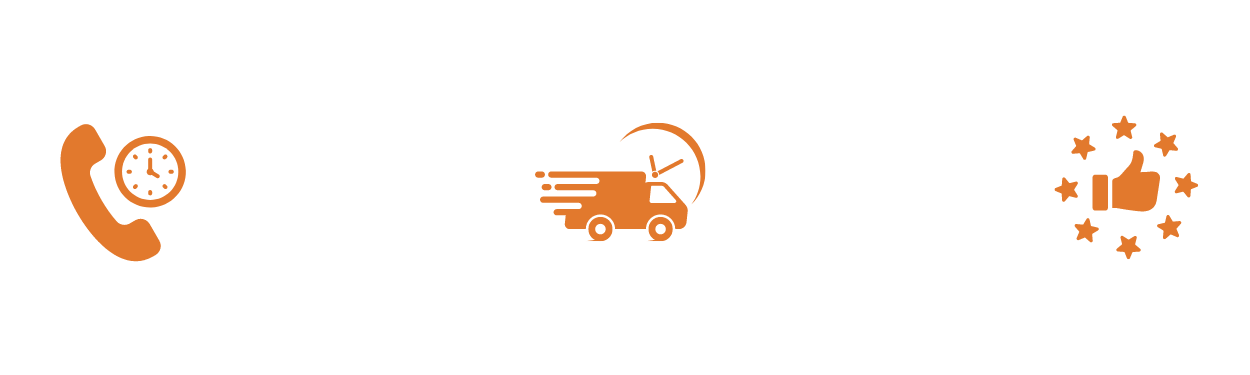
STEP 1
Schedule a Consultation
Start the process by scheduling a consultation call. Discuss your needs and requirements with our experts.
STEP 2
Ship Materials for a Feasibility Study
A feasibility study is placed so that we can test materials using our system. This step ensures you are satisfied with the system’s capabilities.
STEP 3
Your System, Your Way
We customize the system based on your needs and send it to you. Then, you’re all set to conduct inspections on your own.